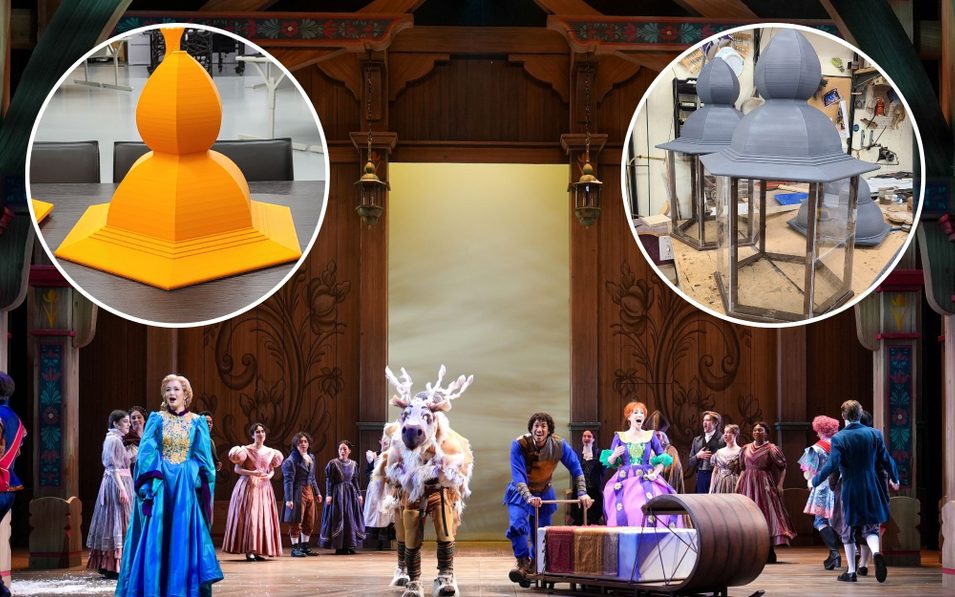
Lighting Up Frozen with 3D Printing
Posted on May 1, 2025
It’s all in the details, especially in a spectacular production like Disney’s Frozen. We had the opportunity to collaborate with local 3D printing company, ExBuild, to create stunning, custom-designed lanterns that enhance the show’s lighting, emotion, and overall theatrical magic!
From hours of printing to their debut on stage, follow the journey of these one-of-a-kind creations and see how technology and artistry come together to help illuminate the world of Frozen!
The 3D Printing Process

ExBuild is a local leader in advanced 3D printing, known for delivering high-quality, custom parts with exceptional precision. Using state-of-the-art printers and expert design techniques, their team helps bring creative visions to life—layer by detailed layer.
For Frozen, ExBuild printed the lanterns in separate parts. The top took one day and forty-seven minutes to print, while the bottom took one day, two hours, and thirty minutes.
“We had a fun project come to us here at ExBuild,” says Sr. Manufacturing Application Specialist Kevin Bork. “Zach [our applications engineer] got a call from [CTC] wondering if we had time for a large project.” To speed up the process, ExBuild looked for ways to simplify the design without losing detail.
“We created an inner shape to reduce material consumption, which also reduced print time,” explains Kevin. “Then in Blade, our slicing software, we used several features to optimize even further.” The result? High-quality, stage-ready parts—delivered on time and within budget.
See the 3D Printing Process in Action
Then the Prop Shop Comes In

“Props for any show set the time, place, social class, and environment of the scenes. It is important for any production to get it right,” says Props Director Sue Brockman, explaining the care and detail that goes into building the world of Frozen on stage.
At CTC, that world-building included the beautiful hand-crafted lanterns seen throughout the show. Shop crew members Chris Engstrom, Joe Cruz, Dave Horn, and Mark Keiffer all worked on different parts of their construction.
Once the 3D-printed pieces arrived, they were assembled using ¼” IPS threaded tubing—commonly used in light fixtures. The top finials were crafted from wood, precisely drilled to allow the tubing to pass through. And the candle-holding glass sections were made from Plexiglass and wood, combining technology and craftsmanship to help bring Arendelle to life.
The Finished Product on Stage!




Come see the lanterns in action along with the rest of the beautifully designed set in CTC’s original production of Disney’s Frozen, on stage through June 22, 2025.